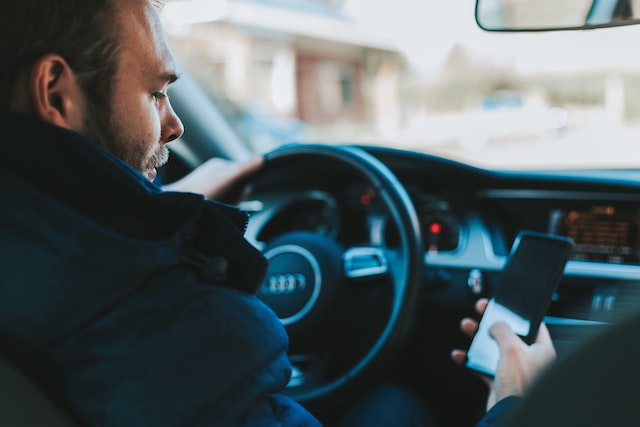
Distracted Driving
Introduction:
Distracted driving is a major cause of motor vehicle accidents and fatalities. According to the National Highway Traffic Safety Administration (NHTSA), distracted driving claimed 3,142 lives in 2019. In this toolbox talk, we will discuss the dangers of distracted driving, the types of distractions that can occur while driving, and ways to avoid distracted driving.
Dangers of Distracted Driving:
Distracted driving is dangerous because it takes the driver’s attention away from the road. This can cause the driver to miss important traffic signals or react too slowly to changes in the driving environment. Distracted driving can lead to accidents, injuries, and even death.
Types of Distracted Driving:
There are three main types of distracted driving:
- Visual Distractions: Visual distractions occur when a driver takes their eyes off the road. This can include looking at a cell phone, texting, reading a map, or applying makeup while driving.
- Manual Distractions: Manual distractions occur when a driver takes their hands off the steering wheel. This can include eating, drinking, adjusting the radio, or using a cell phone.
- Cognitive Distractions: Cognitive distractions occur when a driver takes their mind off the road. This can include daydreaming, talking on a cell phone, or having an emotionally charged conversation with a passenger.
Ways to Avoid Distracted Driving:
There are several ways to avoid distracted driving:
- Put away electronic devices: When driving, it is important to put away electronic devices such as cell phones, tablets, and laptops. If you need to use these devices, pull over to a safe location and use them there.
- Prepare for the trip: Before driving, make sure you are well-rested and have enough time to get to your destination. Plan your route ahead of time and make sure you have any necessary items, such as snacks and drinks, readily available.
- Avoid multitasking: While driving, avoid multitasking such as eating, drinking, or grooming. These activities can take your attention away from the road and increase the risk of an accident.
- Limit distractions: Keep distractions to a minimum by avoiding loud music or engaging in heated discussions with passengers.
- Be a responsible passenger: Passengers should also be responsible and avoid distracting the driver. This includes avoiding loud or disruptive behavior and helping the driver stay alert and focused.
Conclusion:
In conclusion, distracted driving is a major cause of motor vehicle accidents and fatalities. There are three main types of distractions that can occur while driving: visual, manual, and cognitive. To avoid distracted driving, it is important to put away electronic devices, prepare for the trip, avoid multitasking, limit distractions, and be a responsible passenger. By following these tips, we can all do our part to prevent distracted driving and stay safe on the road.